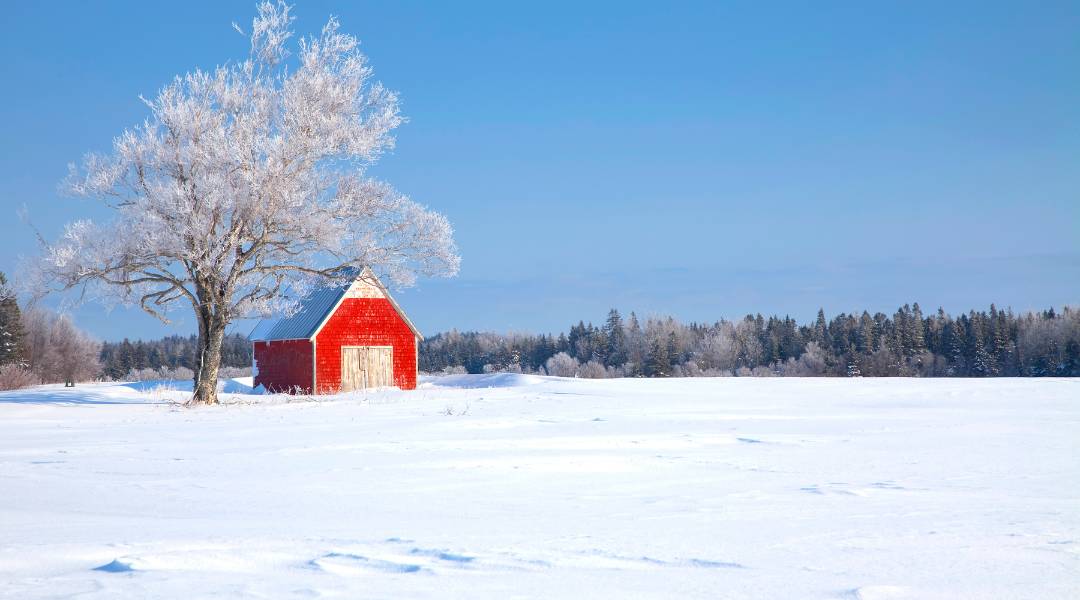
How to Prepare Your Pole Barn for Winter
As winter approaches, your pole barn requires special attention. The chill can wreak havoc on structures with concrete elements if you neglect them. Water freezes and expands within the concrete, risking cracks that compound over time.
Specialty contractors provide restoration to tackle such issues before they escalate into larger problems—a wise move for any property manager looking to save costs long-term. Alongside professional help, regular maintenance checks are vital; this includes ensuring clear roofing drains, which is essential for preventing water damage, which could lead to more significant repairs down the road.
Inspect and Repair Roofing
Begin your winter preparations by inspecting the rooftop of your pole barn. Look for any signs of damage, like cracks or rust, that could let water seep in. Remember, when it freezes, this water expands and wreaks havoc on concrete structures—increasing fractures can spell disaster down the line.
To avoid costly repairs later, address these issues pronto with a specialist contractor’s help—they’re kings at fixing up deteriorating spots before they turn into major headaches. And while you might not think about them much throughout the year, those gutters play a massive role, too; keep them clear to prevent overflow and subsequent foundation trauma from standing water. A little effort now ensures everything stays dry inside—even through New York winters!
Seal Windows and Doors
To keep your pole barn cozy and efficient during chilly months, start by sealing windows and doors. Even the slightest gaps can let cold air invade, spiking your heating costs. Grab weather-proof sealant; a careful application around these openings blocks unwanted drafts.
Regular checks for leaks are wise, too—focus on areas like chimney flashing or pipe boots. Now consider gutters—they’re vital! Ensure they’re clear of leaves or twigs to avoid ice dams that could cause damage over time with rust or corrosion forming from trapped moisture.
By embracing these simple steps, you’ll fortify your steel structure against winter’s bite. You may also trim down energy expenses—a savvy move for any owner looking to preserve their investment without unnecessary maintenance hassles down the road.
Install Proper Insulation
Proper insulation in your pole barn is crucial to keep the cold at bay. Start by considering the structure’s design: with 2×4 or 2×6 lumber for girts, there’s space between these where insulation can fit snugly. While steel panel siding is a common exterior cover, adding OSB sheathing behind it enhances insulating effectiveness and provides support.
Remember that post frame construction—characterized by spaced poles supporting roofs—is prevalent not just in farms but also commercial spaces and even homes. This diversity means well-installed insulation serves multiple purposes from temperature control to energy efficiency across various types of buildings under the “pole barn” umbrella term. Always use quality materials designed to retain heat while keeping winter’s chill out; this ensures comfort inside regardless of how harsh outside conditions may be during colder months.
Clear Gutters Regularly
Focus on the gutters to ensure your pole barn stands strong against winter’s harshness. Clogged with autumn’s fallen leaves, they risk harboring ice that can trigger ceiling leaks when it melts. Remember, maintaining a dry interior is crucial for everything housed inside—from machinery to livestock—and helps preserve structural integrity.
With proper insulation being indispensable, clear gutters play a significant role in preventing moisture from compromising its effectiveness and driving up your energy costs due to heat loss. Moreover, regular gutter maintenance supports overall stability by aiding water diversion away from foundational footings—which must extend below frost lines to avoid upheaval during freeze-thaw cycles.
Enhance Ventilation Systems
As winter approaches, remember that proper barn ventilation is non-negotiable. You’re aiming to keep floors and beds above freezing – simply put, warmer than 32°F avoids ice troubles. High-placed air inputs mixed swiftly preclude cold-induced discomfort for your cows while dodging frozen patches.
Managing dew points below the chilly outside temperatures also means no condensation risks; this ensures dryness where it counts most. With ammonia as a lurking threat to cattle comfort—keep adult levels under 25 ppm and calf spaces even lower at less than five ppm—you safeguard their respiratory health. Chilly weather may sneak up on us, but facing off-season hurdles head-on with high-velocity fresh air and strategically placed fans can prevent freeze-ups efficiently.
Sidestep curtain icing by holding off until temps climb again so they function without fault when you need them most. A tip from experts: active fans don’t always equal effective movement; position them mindfully for maximum impact. Lastly, addressing varied intake points dilutes harmful gas build-up—a crucial step in humidity battles as well—and prevents short-circuiting of airflow, ensuring every corner gets its fair share of freshness all season long!
Prep Your Plumbing Appropriately
When prepping your pole barn’s plumbing for the cold months, always consider preventing frozen pipes. Installing a frost-free hydrant that shuts off water below the frost line is a solid choice—this way, you won’t need to heat entire spaces unnecessarily!
Be cautious with products that may harm plants or animals when draining out of sinks. Avoid cheap options that might break quickly. Alternatively, insulate exposed piping using reliable materials or apply heating tape carefully to maintain flow without freezing issues on colder days.
Protect Foundation from Frost
Securing the concrete temperature is key to shielding your pole barn’s foundation from frost—aim for it to match the ground’s year-round warmth of around 50 degrees. You’re on track with the 2″ EPS foam you’ve got; however, its installation needs careful timing and positioning. Placing foam before setting poles might seem efficient, but it risks damage during drilling.
Here’s a tip: install that sturdy foam about one foot away from where your poles will be—this avoids any accidental punctures or shifts when those big augers spin into action. Directly against the skirting board, add a slim layer of this insulation magic before gently sloping outwards for that crucial one-foot barrier—then let vertical strips dive underground to fortify further. Your contractor has offered an easy solution in theory, yet consider other methods — professionals typically avoid laborious pickaxing by using machinery adept at precise excavation without harming pre-installed elements.
Remember, though, that every site presents unique challenges, so weigh convenience against long-term reliability carefully! As winter rolls in, helping your pole barn stand up to the cold is key. Start by checking for gaps or damage and sealing them tight. Insulate walls and install weather stripping on doors for warmth retention.
Clean gutters prevent ice build-up, which can lead to leaks or collapses. Finally, ensure proper ventilation—it’s essential even during chilly months! Reach out to Woodford Barn Repair—we’ve got you covered when temperatures drop so you can rest easy as the snow falls.